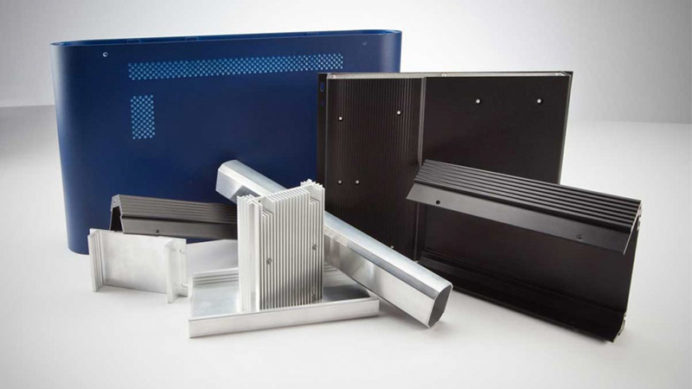
Extrusion is an inexpensive and fast way to create aluminum parts without resorting to extensive machine work. This process takes advantage of aluminum’s high malleability at high temperatures, which means that this metal can be formed into any desired shape without sacrificing the unique attributes it possesses.
Got questions? Contact us today to discuss all your aluminum extrusion requirements.
The Aluminum Extrusion Process
In aluminum extrusion manufacturing, heated aluminum is pushed through a die and cooled back to room temperature. Manufacturers use this process to create parts that incorporate sophisticated cross-sectional profiles. Some post-processing is required for deburring, anodizing, and cutting the extrusion into individual parts, which we describe below.
Understanding Aluminum Extrusions
Extrusion is widely used to make standard parts like tubes and rods as well as custom parts like door and window frames for automobiles. Because of aluminum’s unique ability to withstand high and low temperatures and resist corrosion without weighing too much, many products built via aluminum extrusion tend to be lighter and more durable than similar objects made from other materials.
How Does Aluminum Extrusion Work?
Aluminum extrusion consists of the following steps:
- Aluminum billets are heated to the desired temperature, which is typically 800–925°F. Although aluminum remains solid at this temperature, it is much more malleable here than at room temperature.
- The billets are coated with a lubricant and transferred to a loader. The part that will push the metal through the die, called the ram, is also coated with the lubricant. The lubricant prevents aluminum from sticking to the machine walls and the ram.
- The ram squeezes the heated aluminum through the die, which is shaped in the cross-section of the part being manufactured. When the compressed aluminum emerges from the die, it will take the shape of the die’s hole.
- An extrusion puller guides the extrusion to the runout table, where special saws cut it to the stock length of 150’. The cut stock is transferred to a cooling table to let it reach room temperature. Cooling shrinks the extrusion, which causes it to twist and distort.
- A stretcher is used to straighten the cooled stock. Then, stock pieces are cut the component to its final length. If further hardening is required, the parts are heat treated in artificial aging ovens.
- The parts go through secondary finishing operations like deburring, polishing, and anodizing.
Selecting the Right Aluminum Alloy
Aluminum alloys come with many different properties that enable them to perform well in different applications. Aluminum can be divided into six broad classes of alloys, which are outlined below:
- 1xxx series aluminum alloys resist corrosion very well and possess good machinability and weldability. However, these alloys cannot be heat treated and are not strong. They’re most commonly used for metal spinning and general manufacturing.
- 2xxx series alloys are used to build aerospace components and similar products because they can achieve a high strength-to-weight ratio and have good machinability. However, they do not resist corrosion well, nor are they easily weldable.
- 3xxx series– This alloy type is built with manganese, which raises the aluminum’s strength by 20% while preserving its purity. These types of alloys frequently appear in the food and chemical industries as well as in general manufacturing.
- 5xxx series resists corrosion very well, and it also possesses good formability, strength, and weldability, which make it ideally suited for use in marine environments. However, 5xxx series alloys do not respond well to heat treatment.
- 6xxx series is the most prevalently used series of aluminum alloys. It’s a highly weldable alloy found in many architectural and structural settings. This alloy can also be easily anodized, which lets manufacturers pair it with different finishes. Many coupling and hardware applications make use of this aluminum alloy.
Custom Aluminum Extrusions
Benefits of Custom Extrusions
Because pure aluminum tends to be too soft for industrial use, manufacturers frequently alloy it with other materials to enhance specific attributes of the alloy, as demonstrated above. Extruded products can be built with diameters of up to 15”, and most extruders offer extruded aluminum in standard seamless tubes, rods, bars, and plates as well as custom options.
This infinite customization capability allows aluminum extrusion clients a great degree of control over the specifications they wish to incorporate in their end product.
Uses and Applications
When combined with aluminum’s ability to perform well in the extruding process, the above traits make aluminum the material of choice for custom projects. Aluminum alloys perform well in a number of secondary options after the extrusion process, such as:
- Machining
- Grinding
- EDM cutting
- Tempering
- Welding
Once secondary operations are complete, extruded products can be treated to a number of finishing processes as well. Some popular finishing options are:
- Anodizing
- Electroplating
- Painting
- Powder coating
- Printing
- Labeling
Full-Service Aluminum Extrusion from Tanfel
Tanfel has been a leading provider of custom metal parts since 2008. We specialize in working with our customers on all aspects of manufacturing, from design to global logistics.
Here is an overview of Our Aluminum Extrusion Capabilities/Services:
- Aluminum (1xxx, 2xxx , 3xxx , 5xxx , 6xxx , 7xxx) series
- Circle / Diameter: Up to 15 inches
- Seamless Tube, Rod, Bar, Plate, and Custom parts
- Secondary operations: Machining, Grinding, EDM cutting, Heat treating / Stress relieving, Welding,
- Finish: Anodizing, Electroplating, Painting, Powder coating, Printing / Labeling
Where most other aluminum extrusion firms complete their process after the raw production phase, we at Tanfel provide full-service finishing services as needed. Once we’re finished with your order, you can directly use it in whatever application you need it for.
Contact us today to request a quote for all your aluminum extrusion requirements.