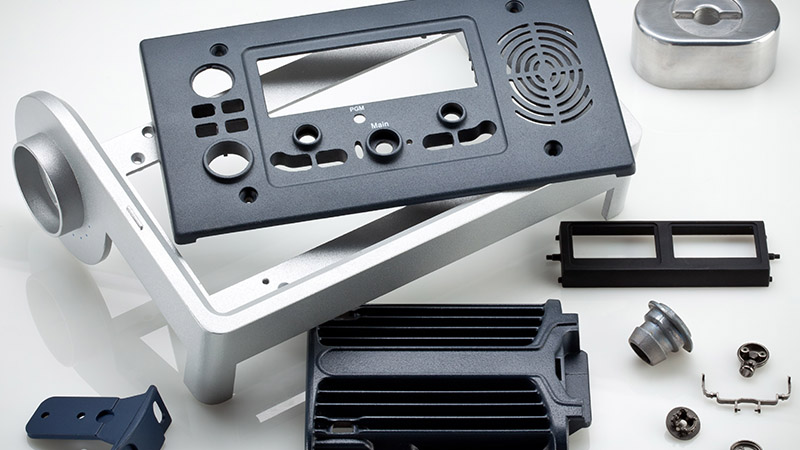
Metal casting creates high-quality, reliable parts. Selecting the appropriate casting process depends upon the design, metal selection, and surface finish needs.
Tanfel Custom Metal Parts can help you select the right metal casting process from popular methods such as sand casting, investment casting, and die casting.
The Metal Casting Process
Metal casting is a metal forming process that creates precise metal shapes by pouring molten metal into a mold. This method of producing metal parts been used for centuries and remains in use today, creating products ranging from train wheels to lamp posts.
Before the metal is cast, engineers must design a pattern that represents the outside of the object being created. They must also create a core if the item will be hollow, such as a cup or a product casing. Next, engineers create the mold itself.
During the casting process, metalworkers melt down metals and alloys until they become a molten liquid. The molten metal is poured into an expendable mold or a permanent mold.
- Expendable molds are made from materials such as sand or ceramic. Once the cast has cooled, the mold can be destroyed to free the metal part.
- Permanent molds can be reused for simple shapes that facilitate easy and damage-free extraction.
Once the metal is poured into a mold, it cools and hardens into a solid shape. The material is typically left to cool naturally, but may also be cooled with water once it reaches a sufficiently semi-solid state. If the metal has a sand-based mold, the cooling process will also include a vibration stage to keep sand out of the metal. Metalworkers often perform additional processes, such as finishing or cleaning, after the workpiece is removed from the mold.
Advantages of Casting Metal
Casting metal offers a number of benefits. These advantages include:
- Single-piece products. Metal casting allows for the production of seamless metal parts for consistent strength and product integrity
- More design options. Well-designed molds allow metalworkers to create complex and/or hollow shapes.
- Almost all metals can be used to produce castings.
- Low waste. Metal casting creates near-perfect shapes with little wasted material. Excess sand from molds and excess molten metal can be cooled and reused.
- Cost-effectiveness. As a low-waste, relatively straightforward process, manufacturers can produce metal parts at a lower per-unit cost than some competitive manufacturing methods.
All of these advantages apply to the variety of metal casting methods available for prototype and large production runs.
Choosing the Best Casting Process for Your Needs
Multiple casting processes are available and each has been fine-tuned to best fit specific metals, molds, and end products. Before ordering a specific metal casting process, it’s essential to examine the options available to make sure you’ve selected the appropriate method. We also recommend consulting with an industry expert to ensure you choose the best metals and casting process for your particular design specifications.
Types of Metal Casting Processes
Investment casting, sand casting, and die casting are the three most common metal casting processes. Each has its own advantages and produces metal parts with different levels of complexity and cost.
Investment Casting
Investment casting—or precision casting—uses specialty wax molds to create highly detailed and intricate models that capture every detail of the design. Mold creators then encase the wax in ceramic to create a longer-lasting mold that can be used multiple times without degradation. This casting process can be used to create steel and stainless steel metal parts.
Advantages of this casting process include:
- Intricate, highly-detailed end products that require minimal finishing or detailing
- Smooth surface finishes
- Cost savings due to reusable molds
- Accuracy in terms of dimensionality and surface details
Sand Casting
In sand casting, molds are made from mixtures of sand and clay. Builders pack the sand and clay mixture over an existing model or pattern to give it structural integrity before the molten metal is poured into the mold. Once the metal hardens, metalworkers can break away the sand to extract the metal piece.
Sand casting offers advantages such as:
- The sand can be reused, so there is little material waste
- May be used to create large molds and castings
- Has a low cost during the casting process and tooling stages
- Sand casting works well with a variety of ferrous and non-ferrous metals
Die Casting
Die casting uses tool steel molds to create castings from softer metals like zinc and aluminum. Each mold comes in two parts that fit together so the mold can be safely removed for reuse once the casting hardens.
Manufacturers use die-casting processes for small and intricate pieces that need to be produced in large quantities or over a long period of time. Instead of pouring the metal, manufacturers force the metal into the mold at pressures of up to 25,000 psi, ensuring that it entirely fills the mold before it starts to cool and harden.
Advantages of die casting include:
- Manufacturers can produce intricate parts with thin walls and fine features
- Production is fast and cost-effective
- Finished products have a high degree of stability and dimensional accuracy, as well as a good surface finish
The Key Differences Between Investment Casting, Sand Casting, and Die Casting
While every casting method has its advantages, not every method is suitable for any metal casting order. Some of the most important factors to consider are:
- Dimensional accuracy. Parts that need to be built to meet tight tolerances and stringent specifications should use die casting or investment casting processes. Sand casting has a lower dimensional accuracy.
- Part size. Die-casting typically handles small parts, whereas sand casting can create very large parts.
- Surface finish. Die-casting creates the smoothest and most accurate surface finish, with investment close behind. Sand casting produces parts that require the most surface finishing, especially for highly detailed pieces and ferrous metals.
Common Industrial Applications
Approximately 90% of manufactured goods and machinery have cast parts or components. Every industry uses metal casting processes or products manufactured through metal casting. Some of the most common industrial applications include:
- Electrical equipment: Compressors, generators, motors, and pumps
- Heavy equipment and transportation vehicles: Automobiles, airplanes, farming and mining vehicles, trains, and ships
- Industrial machinery and hardware: Casting, forging and extrusion tools, plant machinery and tools, valves, and fittings
Materials: Commonly Used Alloys for Casting
Different metal casting processes allow designers to choose from a wide range of metals and alloys. Some of the most commonly used metal alloys include:
- Steels: Carbon steel, 300 and 400 series stainless steel, precipitation hardened stainless steel, low-alloy steel, and tool steel
- Alloys: Aluminum alloys, cobalt-based alloys, and nickel-based alloys
If your product requires a specific type of metal, it’s essential to match that metal selection to the best casting process.
Casting Finishes
Each casting method produces different surface finishes or textures. The three elements that measure a surface’s finish include its lay, waviness, and roughness. The best metal casting method for excellent surface finish is die casting, which produces smooth and precise parts. Conversely, sand casting typically produces rough surface finishes. Investment casting falls in between the two extremes.
Custom Casting Parts from Tanfel
Tanfel can help cast your precision metal parts using a variety of casting methods. We offer sand, investment, and die casting services, as well as surface and other metal treatment services. We have ISO certified facilities around the world to complete all of your metal casting and other metalworking project needs quickly. Contact our team or request a quote to learn more about the custom metalworking services we offer.